News / Tech News |
Unconventional technology enhances composites important to automotive, aerospace and renewable energy industries
Scientists at the Department of Energy’s Oak Ridge National Laboratory have developed a method that demonstrates how fiber-reinforced polymer composite materials used in the automotive, aerospace and renewable energy industries can be made stronger and tougher to better withstand mechanical or structural stresses over time.
This graphic shows an unconventional approach to making widely used composite materials stronger and tougher. Thermoplastic fibers are deposited like cobwebs on top of rigid fibers to chemically form a supportive network with a surrounding matrix, or binder substance. Photo: Adam Malin/ORNL, U.S. Dept. of Energy
The composites already have many good things going for them. They are strong and lightweight relative to their metallic counterparts.
They are also corrosion and fatigue resistant and can be tailored to meet specific industrial performance requirements. However, they are vulnerable to damage from strain because two diverse materials — rigid fibers and a soft matrix, or a binder substance — are combined to make them.
The interphase between the two materials needs to be improved because of its influence on the overall mechanical properties of the composites.
ORNL’s Sumit Gupta said the research team deposited thermoplastic nanofibers like cobwebs to chemically create a supportive network that toughens the interphase.
Their technique differs from conventional methods of coating the fiber surfaces with polymers or providing a rigid scaffolding to improve bonding between the fiber and the matrix, which have been shown to be inefficient and expensive.
Gupta said he and the team carefully selected the nanofibers and matrix material to create high-surface-area scaffolding or bridging as a load transfer pathway, a mechanism through which stress is passed between the reinforcing fibers and the surrounding matrix material.
“Our process enables the material to withstand greater stress. By using this simple, scalable and low-cost approach, we are able to increase the strength of the composites by almost 60% and its toughness by 100%,” he said.
Composites manufactured with such an advancement could improve countless things applied in our daily life, from vehicles to aircraft.
“Once we knew the basic science and the chemistry behind what we’d developed, we became confident we had valuable applied technology,” said ORNL’s Christopher Bowland.
“Pioneering new technology and understanding fundamental science is one aspect of the work we do. Still, another facet of applied research is to explore how the technology can be translated to real-world applications to benefit society. Working with ORNL’s Technology Transfer team, a patent has been filed on this research to potentially translate the technology to commercial partners.”
Bowland said future research lies in different fiber and matrix systems that have compatible chemical groups, and the researchers plan to perform more studies on the nanofibers themselves to increase their strength.
This study is part of the newly established Composites Core Program 2.0 from the Materials Technology Program. The program, led by ORNL along with participating labs Pacific Northwest National Laboratory and the National Renewable Energy Laboratory, strives to enhance vehicle efficiency through advanced materials development.
“One route to achieve the program’s objective is to replace heavier steel components with carbon fiber composites, which currently offer the best weight-reduction potential,” said Amit Naskar, leader of ORNL’s Carbon and Composites group.
“Developing stronger and tougher interphases in high-performance fiber-reinforced composites can reduce fiber volume fraction with improved mass reduction and subsequent cost-effectiveness of the composite structures.”
The research team used resources of the Compute and Data Science user facility at ORNL for computational studies to understand the fundamental bonding forces.
The team also employed atomic force microscopy at the Center for Nanophase Materials Sciences, or CNMS, to characterize the stiffness or rigidity of the designed interphase.
YOU MAY ALSO LIKE

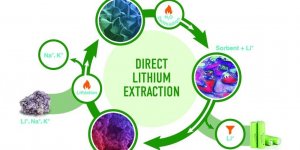










